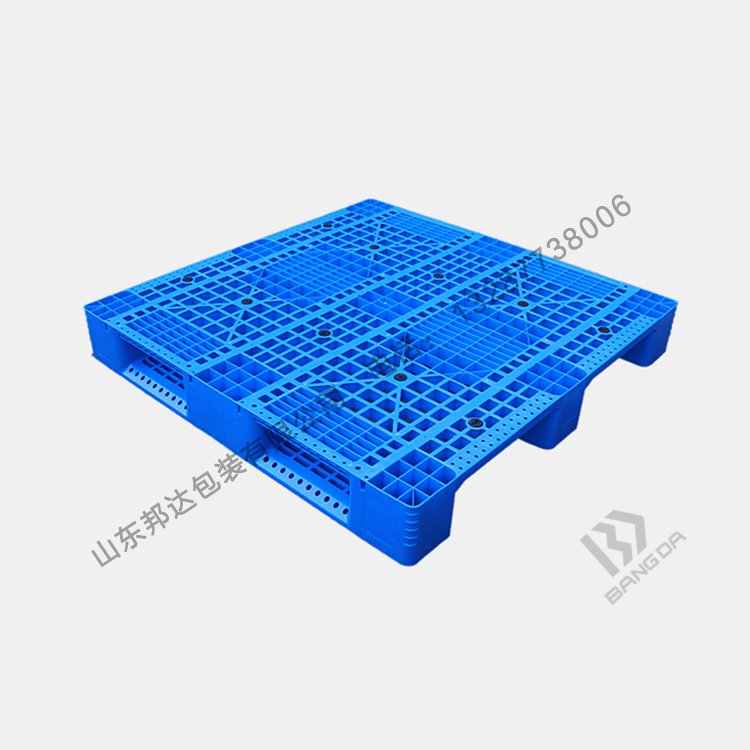
除了考虑塑料托盘内外表面的温度趋于平衡外,还应考虑塑件各侧的温度一致,即模具冷却时要尽量保持型腔、型芯各处温度均匀一致,使塑件各处的冷却速度均衡,从而使各处的收缩更趋均匀,有(yǒu)效地防止变形的产生。因此,模具上冷却水孔的布置至关重要。在管壁至型腔表面距离确定后,应尽可(kě)能(néng)使冷却水孔之间的距离小(xiǎo),才能(néng)保证型腔壁的温度均匀-致。
同时,由于冷却介质的温度随冷却水道長(cháng)度的增加而.上升,使模具的型腔、型芯沿水道产“生温差。因此,要求每个冷却回路的水道長(cháng)度小(xiǎo)于2m。在大型模具中应设置数条冷却回路,一条回路的进口位于另一回路的出口附近。对于長(cháng)条形塑件,应采用(yòng)冷却回路,减少冷却回路的長(cháng)度,即减少模具的温差,从而保证塑件均匀冷却.
塑料托盘塑化阶段对制品翘曲变形的影响
塑料托盘塑化阶段即玻璃态的料粒转化為(wèi)粘流态,提供充模所需的熔體(tǐ)。在这个过程中,聚合物(wù)的温度在轴向、径向(相对螺杆而言)的温差会使塑料产生应力;另外,注射机的注射压力、速率等参数会极大地影响充填时分(fēn)子的取向程度,进而引|起翘曲变形。
注射的初期使用(yòng)低速,模腔充填时使用(yòng)高速,充填接近终了时再使用(yòng)低速注射的方法。通过注射速度的控制和调整,可(kě)以防止和改善制品外观如毛边、喷射痕、银条或焦痕等各种不良现
多(duō)级注射控制程序可(kě)以根据流道的结构、浇口的形式及注塑件结构的不同,来合理(lǐ)设定多(duō)段注射压力、注射速度、保压压力和熔胶方式,有(yǒu)利于提高塑化效果、提高产品质量、降低不良率及延長(cháng)模具/机器寿命。
通过多(duō)级程序控制注塑成型机的油压、螺杆位置、螺杆转速,能(néng)谋求改善成型件的外观不良,改善缩水、翘曲和毛边的对应措施,减少各模每次注射成型件的尺寸不均。
塑料托盘脱模阶段对制品翘曲变形的影响
塑件在脱离型腔并冷却至室温的过程中多(duō)為(wèi)玻璃态聚合物(wù)。脱模力不平衡、推出机构运动不平稳或脱模顶出面积不当很(hěn)容易使制品变形。同时,在充模和冷却阶段冻结在塑件内的应力由于失去外界的约束,将会以变形的形式释放出来,从而导致翘曲变形。
计算残余应力和最终形状(收缩和翘曲)。他(tā)们考虑了保压阶段的影响,将制品分(fēn)成三层,由三维网格来分(fēn)析残余应力和变形。,提出了 在保压阶段以后所引起的残余应力和变形的数值模拟模型。计算残余应力时,采用(yòng)了热粘弹模型(包含體(tǐ)积松弛)。其采用(yòng)的有(yǒu)限单元法是基于由平面单元集合而成的壳层理(lǐ)论,该理(lǐ)论正适用(yòng)于形状复杂的薄壁注塑制品。